NOTICE: General Reference Only
The information provided in this article is
for general reference purposes only and does not constitute project-specific guidance. SLD Technology products are engineered to order, and their installation must comply with all applicable codes, standards, and project-specific specifications. In all cases, the
approved project documentation and requirements take precedence over any general information contained herein. For project-specific instructions, contact your SLD Project Manager or the SLD Support Team at:
support@sldus.com.
Introduction
Welcome to the
AirFRAME® Installation Manual, provided by
SLD Technology, Inc. This manual offers step-by-step instructions to help ensure the safe, accurate, and efficient installation of your AirFRAME ceiling system. For additional resources, including other product-specific manuals, please visit our online Knowledge Base at
www.sldus.com/support or contact the SLD Support Team at
support@sldus.com.
NOTICE: Training Available for Installers
IMPORTANT NOTE: Product-Specific Manual
This installation manual is intended specifically for
AirFRAME® ceiling systems. Other SLD products such as LEDiffuser®, uLED™, and AirFRAME-LT® (for example) each have their own installation manuals and procedures. Always refer to the correct manual for the specific product being installed. For assistance, contact your SLD Project Manager or the SLD Support Team at:
support@sldus.comSafety Precautions
- Read All Instructions: Review this manual in full before beginning any installation or maintenance activities.
- Required Training: All personnel must be trained on this equipment and applicable safety procedures prior to beginning work.
- Qualified Personnel: Installation and maintenance must be performed by trained and qualified professionals. To arrange training, [Click Here] or email support@sldus.com.
- Lockout/Tagout (LOTO): De-energize and lock out all power sources before servicing or handling electrical components. Follow OSHA-compliant LOTO procedures (29 CFR 1910.147 or current applicable standard).
- Electrical Testing: Use an appropriately rated voltage tester to verify all circuits are de-energized before performing any electrical work.
- Tool Use and Inspection: Use only tools in good condition that are appropriate for the task. Inspect all tools before use and remove damaged or worn tools from service.
- Personal Protective Equipment (PPE): Wear safety glasses, gloves, safety-toe boots, and any additional PPE required by task-specific hazards or the jobsite safety plan.
- Fall Protection: When working at height, use approved fall arrest systems in accordance with OSHA fall protection standards (29 CFR 1926 Subpart M or current applicable standard). Ensure all anchor points, harnesses, and connectors meet required ratings.
- Secure Work Area: Establish and clearly mark an exclusion zone around the installation area to prevent unauthorized entry and protect personnel from overhead and operational hazards. Use barricades, warning signage, or spotters as needed. Enforce this zone throughout the duration of the work.
- Material Handling: Stack and store materials in a stable, secure manner to prevent tipping, sliding, or collapse. Do not store materials in a way that obstructs walkways, access panels, emergency equipment or emergency exits.
- Lifting Precautions: Use only mechanical lifting equipment rated for the load; do not attempt to manually lift or support AirFRAME modules. When handling smaller components or preparing equipment for lifting, use proper body mechanics and ergonomics to avoid strain. When working at height, use appropriate fall protection and secure all materials. Always ensure the area below is clear of personnel before lifting, moving, or lowering equipment overhead.
- Lifting Equipment Ratings: Ensure all rigging, hoists, slings, and lifting equipment are rated for the load being lifted. Do not exceed the rated capacity of any lifting device or attachment.
- Work Environment: Ensure the installation area is clean, dry, well-lit, and free of dust, debris, or other environmental hazards. Verify adequate ventilation and lighting are in place before beginning work.
- Housekeeping: Maintain a clean and organized work area. Immediately clean up spills and remove debris to prevent slip, trip, fall, and crush hazards.
- Confined Space Awareness: Do not enter enclosed ceiling spaces or plenums unless authorized and trained. Follow OSHA-compliant confined space entry procedures, including ventilation and monitoring if required.
- Emergency Procedures: Know the location of first aid kits, fire extinguishers, emergency exits, and all site-specific emergency protocols. Report all injuries, incidents, and near misses immediately in accordance with site policy.
WARNING: Failure to Follow Safety Precautions May Result in Serious Injury or Death
All installation and maintenance activities must comply with applicable
OSHA, ANSI, and
local safety regulations. Only
qualified personnel should perform work on or around AirFRAME systems. Follow all instructions in this manual, and adhere to proper
lockout/tagout procedures, personal protective equipment (PPE) requirements,
lifting safety, and
environmental controls. Improper handling or installation may result in
electrical shock, falls, equipment damage, or
hazardous exposures. Refer to project-specific safety plans and site protocols. For questions or clarification, contact your SLD Project Manager or the SLD Support Team at:
support@sldus.com before proceeding.
System Description
The AirFRAME modular operating room (OR) ceiling system integrates all OR ceiling-mounted components — including ventilation, filtration, integral lighting, and other electrical components, as well as mounting plates, rails or other connection points for medical gas, audio visual, equipment/ lighting booms, and imaging equipment — into factory-assembled modules. The modules are installed as a complete system instead of following the linear process of installing each of these items individually, as is the case with traditional stick-built construction. Components potentially included with the AirFRAME system include:
- AirFRAME (AF) airflow modules
- Outboard (OB) equipment mounting modules
- Rail Channel (RC) rail mounting modules
- Hinged Damper-Diffuser (DD) assemblies
Installation Contractor Training
NOTICE: Qualified Installation Required
AirFRAME systems must be installed only by contractors trained and authorized by SLD Technology, Inc. Due to custom configurations and project-specific requirements; installation procedures may vary between jobs. Contractors are strongly advised to schedule a training session with SLD Technology prior to shipment.
Failure to complete proper training may result in improper installation, project delays, or safety hazards. To arrange training, schedule through the online portal at
www.sldus.com/support or contact the SLD Support Team at:
support@sldus.com.
Installation Contractor Training:
Supply, Install, and Connect (SIC) Responsibility Matrix
Table 1 represents the responsibility matrix for a typical AirFRAME ceiling system installation. Please note that every project is unique, and that this flow can change from region to region, or for a whole host of other reasons. The actual flow for a given project is determined by the general contractor.
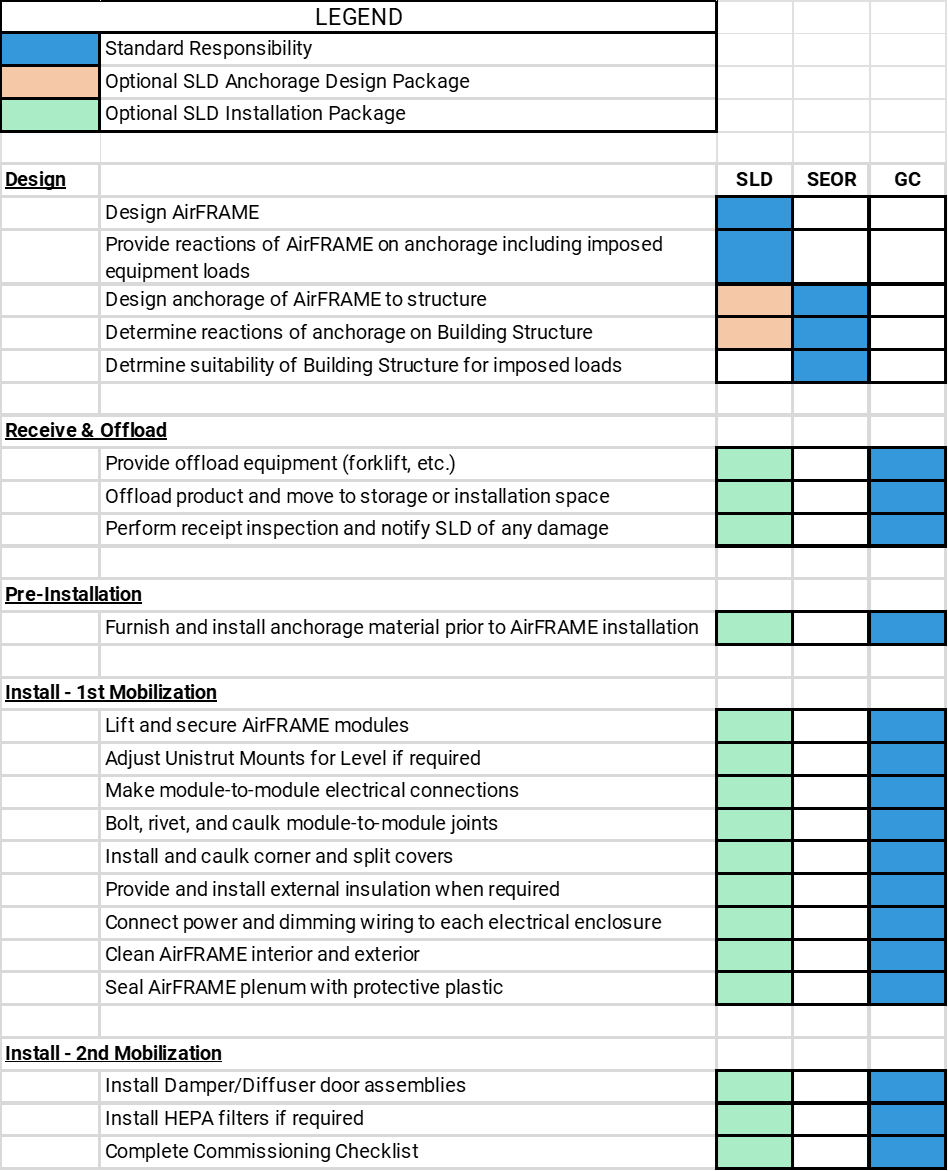
Table 1: SIC Matrix
NOTICE: SIC Matrix - Typical Flow
The actual flow for your job or project may vary based on the region, requirements of the job, or other factors. Contact your SLD Project Manager or the SLD Support Team at:
support@sldus.com.
- Read this manual thoroughly before unpacking, installing, or operating the AirFRAME system.
- To prevent damage, do not move modules into the operating room (OR) until all demolition, pre-construction, and clean-up activities in the space are complete.
- Do not unwrap modules until they are ready for immediate installation.
- Inspect the exterior wrapping of each module for factory-applied tags identifying the specific OR where each module is to be installed.
- Verify module tags against the ship loose drawings to confirm location and orientation. There is a physical unit tag that is typically located on the southwest corner of each module (as shown on the ship loose drawings) and include the job number, room identification, and module designation.
- Verify that the electrical and mechanical connection points of the AirFRAME system match the drawings and will be accessible before and after installing modules.
- Modules are not interchangeable—do not mix & match components between room designations.
- Before installation, confirm that the electrical and mechanical connection points match the drawings and will be accessible both during and after installation.
- SLD Technology recommends covering the diffuser and supply air openings during construction to prevent debris or dust from contaminating the air delivery area or collecting in diffuser screens and dampers.
- Do not install filters (if applicable) until all construction is complete and the OR is ready to be commissioned.
- The unit openings (diffuser and supply air) shall be covered during construction to avoid entrapment of dust and/or debris inside the air delivery area and/or in diffuser screens and dampers.
- DO NOT install filters (if applicable) until all construction is complete and the OR is ready to be commissioned as an OR.
WARNING: Lifting, Pressurization, and Electrical Hazards
Installing and servicing the AirFRAME® modular fully-integrated OR ceiling system may involve
lifting, system pressure, and electrical hazards. Only
trained and qualified personnel experienced in the installation of similar systems should install or service AirFRAME equipment.
Click Here for Training Information or contact
support@sldus.com.
WARNING: Electrical Shock Hazard
Before connecting the AirFRAME® system to power or servicing any electrical components, always turn off and lock out all power sources in accordance with OSHA-compliant Lockout/Tagout procedures. There may be multiple disconnect switches. Failure to de-energize and secure all power sources may result in serious injury or death from electrical shock.
NOTICE: Code Compliance Required
AirFRAME systems must be installed in accordance with: National Fire Protection Association (NFPA) standards, the National Electrical Code (NEC) and all applicable local building and electrical codes. Consult the authority having jurisdiction (AHJ) prior to installation to ensure compliance with local regulations.
INSTALLER TIP: Handle Long-Lead Items with Care
The hinged Damper-Diffuser (DD) assemblies and HEPA filters are expensive, long-lead components. Store these parts in a clean, secure location and handle with care to avoid damage or installation delays.
- Forklift or Telehandler with long forks or fork extensions (≥6 feet)
- Impact gun, drill or driver with #2 Phillips bit
- Forklift or Telehandler to move Modules off of shipping pallet to Staging Blocks or Moving/Furniture dollies (heavy duty recommended).
- Moving Dollies
- Standard Furniture Dollies
Sufficient for one-time or minimal use
INSTALLER TIP: AirFRAME® modules weigh 300-1800lbs; standard dollies may wear out quickly due to bearing stress.
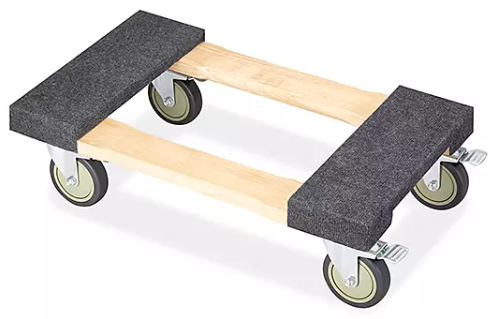
Figure 1: Standard Moving Dolly
Recommended for repeated use.
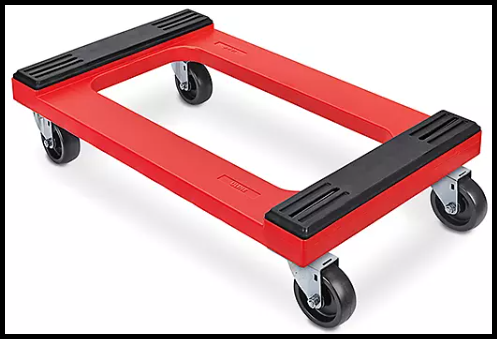
Figure 2: Heavy Duty Moving Dolly
- Low Profile Heavy Duty Dollies
Highly recommended for larger projects or repeat installations.
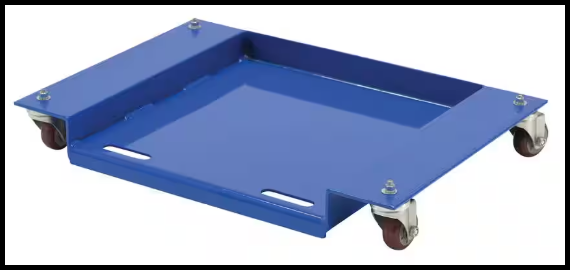
Figure 3: Low Profile Heavy Duty Moving Dolly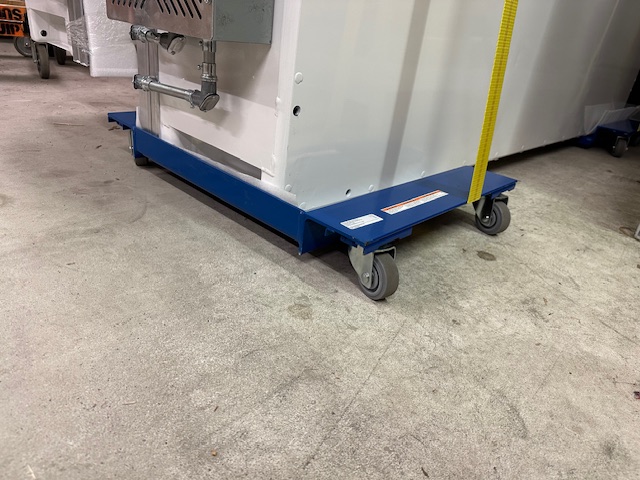
Figure 4: AirFRAME® module on Low Profile Heavy Duty Moving Dolly
- 2x4 and 4x4 wood blocks (can use blocks off shipping pallets)
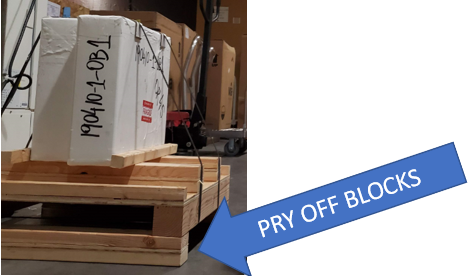
Figure 5: AirFRAME® modules on shipping pallet
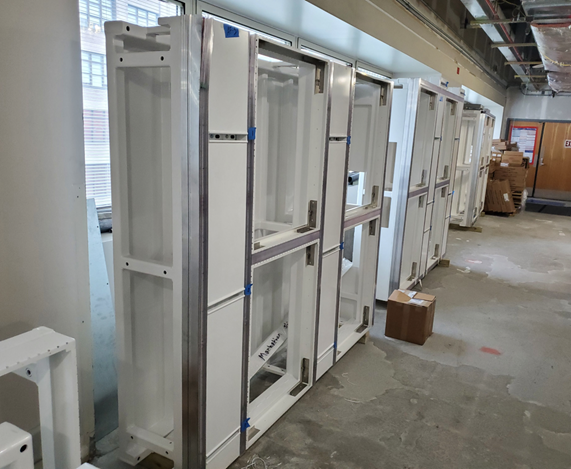
Figure 6: AirFRAME® modules on blocks
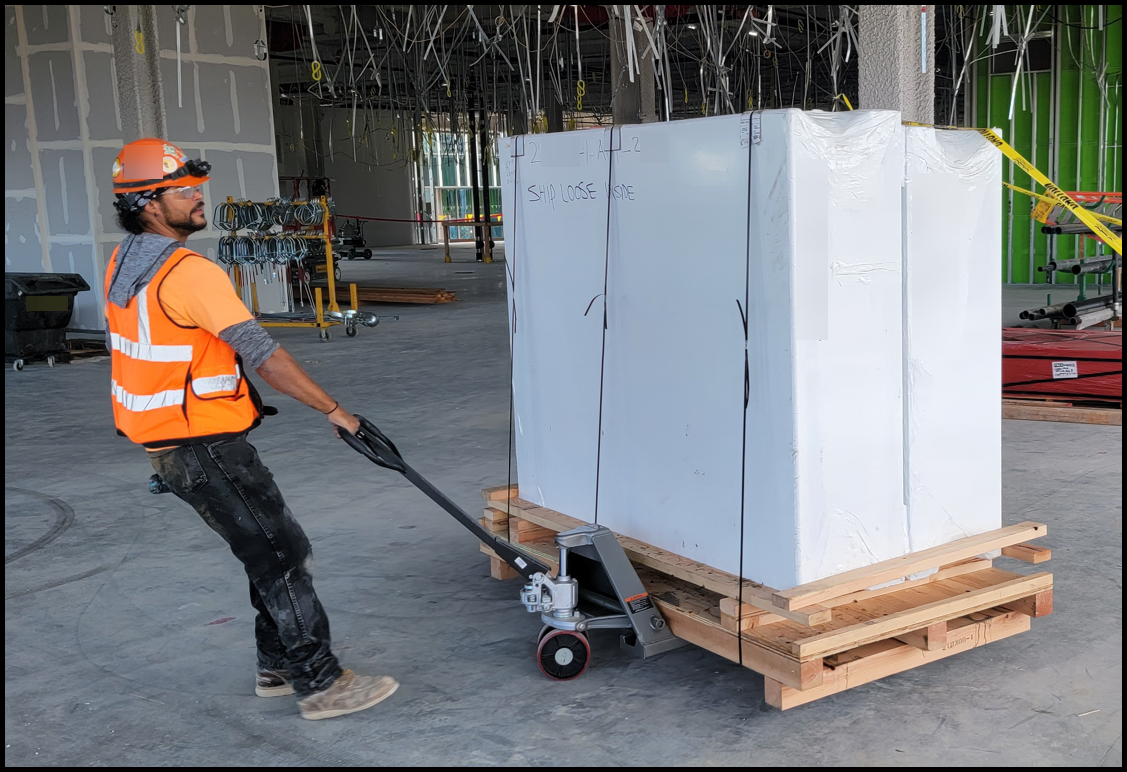
Figure 7: Shipping pallet on pallet jack
- Material Lifts (minimum 2 required. Modules weigh 300-1800lbs each. For verified module weights, reference the project submittal, contact your SLD Project Manager or email support@sldus.com)
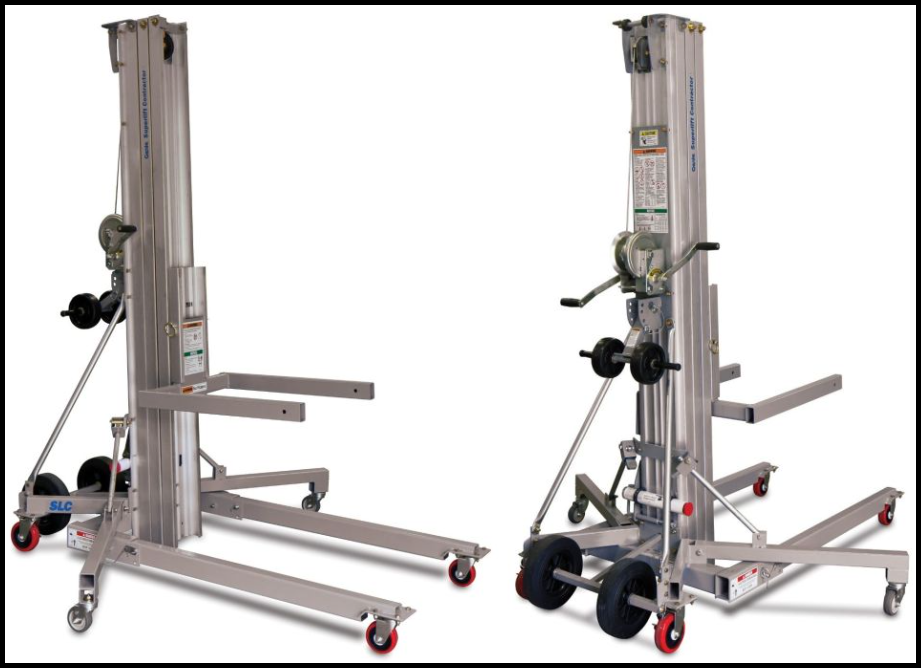
Figure 8: Material Lifts
- Chain Hoists (2 recommended, 1 minimum)
- Ladders
- 4 total recommended: mix of 8 ft and 10ft ladders
- At least one 10 ft ladder is recommended
- Plastic sheeting and vinal tape (for protecting unit once initial install is complete)
- Self-leveling Laser Level (for verifying hanging height)
- Hand Tools:
- Spirit or Digital Level (>3ft recommended)
- Sockets and Wrenches (SLD Ship Loose Hardware is Imperial)
- Wrench 15/16" for 5/8" suspension hardware (ratcheting/speed wrench recommended)
- Impact gun, drill, driver
- 3/4" socket for 1/2" module-to-module hardware
- #2 Phillips driver bit for self-tapping screws
- 5/16" driver bit for self-tapping screws
- Wrench 3/4" for 1/2" module-to-module hardware
- Tape Measure (calibrated)
- Drift Pin (for module-to-module alignment)
- Utility Knife
- Pry Bar
- Rubber Mallet
- Rivet Gun (for 1/8" rivets)
- Caulking Gun
- Wire cutters/stripers
- Torque Wrench with lower limit of at least 23ft-lbs [31.18 newton-meters] (for rooms with Imbedded Unistrut only)
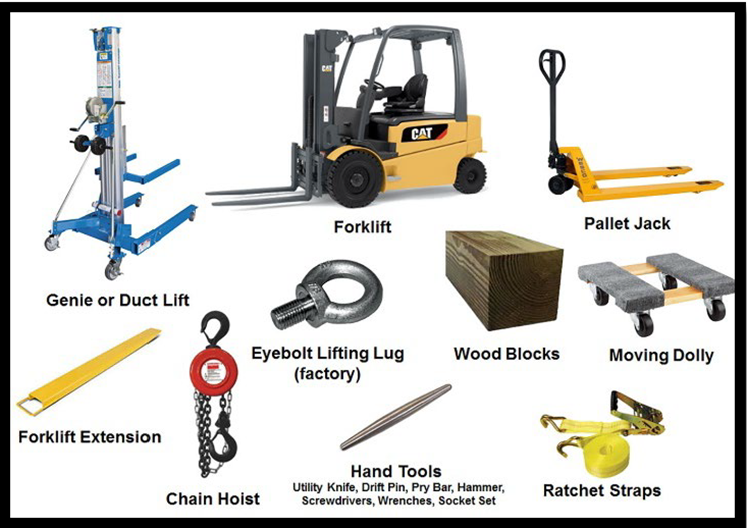
Figure 9: Tools needed
INSTALLER TIP: Helpful Tool Suggestions
3-in-1, hammer, spud wrench, and drift pin in one:
Ratcheting/speed Wrench 15/16" for 5/8" hardware
Site Survey and Environmental Conditions
Move-in Path Assessment
Before delivery and installation, walk the entire move-in path and measure the minimum height clearance. Reference the tallest AirFRAME module from the project submittal and ship loose drawings. In addition to the module height, here may be a 4-inch deep electrical enclosure attached to the module as well as any of the the following site constraints to consider:
- Electrical Enclosures and or J-boxes physically attached to the AirFRAME
- Furniture Dolly height (largest module PLUS dolly height) - see Tools and Materials section. Low-profile dollies are recommended for tall modules
- Floor trim and door trim
- Automatic door closing arms
- Access Control locks or other over-door hardware
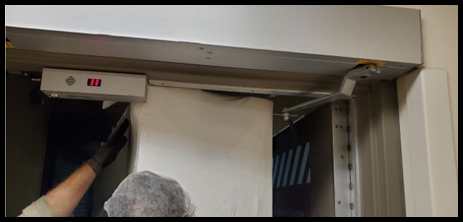
Figure 10: Doorway conflict example
Suspension Point Locations
Before lifting any modules, verify that the suspension point hangers, typically 5/8" All-Thread Rod (ATR), are placed and secured correctly in the room according to the project-specific
Structural Calculations, interstitial framing design as well as the suspension point page of the ship loose drawings. All rods must be in place and secured to the structure before lifting modules.
NOTICE: Always Verify Orientation
"Plan North" does not always match "True North" on a compass.
INSTALLER TIP: Pre-thread a top nut and fender washer onto each rod. Tape the washer to the nut to keep it in place during lift-in.
Figure 11: Whole room prepared hanging rods
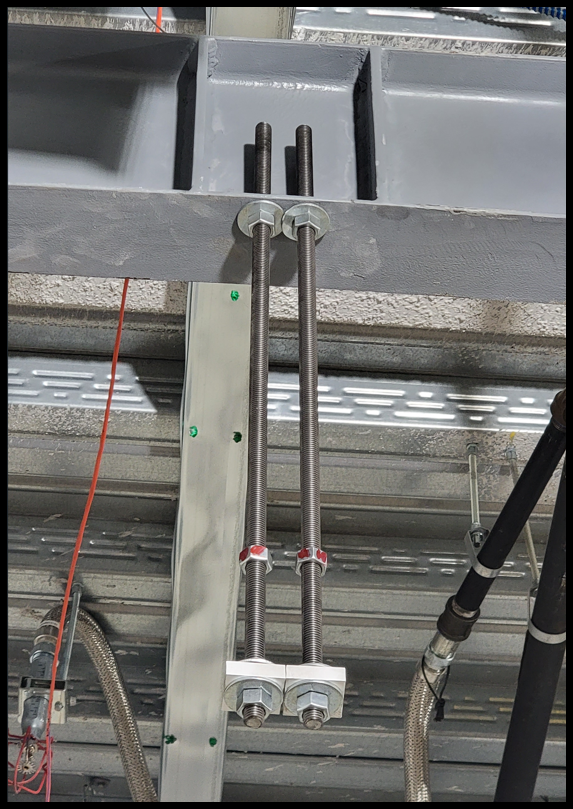
Figure 12: Prepared hanging rods
ALERT: Anchoring and Bracing Responsibility
Materials and design for anchoring and lateral bracing are not typically within SLD Technology's scope, by others. Refer to the Structural Engineer of Record SEOR for framing, anchorage and bracing requirements.
For assistance, contact SLD Support at:
support@sldus.comCeiling Height Verification
The AirFRAME suspension elevation is CRITICAL — especially in Hybrid ORs where ceiling-mounted imaging systems are involved. Some manufacturers (Phillips, Siemens, Canon, etc.) allow less than 4-6mm of height tolerance.
REQUIRED: Verify Finished Ceiling Height
Ceiling height must be verified and clearly marked (scribed) in the room. Coordinate with the GC, Architect, and Engineer prior to AirFRAME installation. This scribe point is by others and not within SLD Technology's scope.
IMPORTANT NOTE: Measuring from Concrete Floor Unreliable
Measuring from the concrete floor at installation can lead to issues with ceiling height in the future. Concrete floors during construction are usually not level and the finished floor can add inches in height. Remember to take into account the finished floor thickness.
INSTALLER TIP: Laser Level Usage
Use a self-leveling laser level (ensure it is not in locked/manual mode) to measure ceiling height.
- Place the laser level at the final ceiling height, or
- Set the laser at a known distance below the target height and use a tape measure to measure upward.
General Operating Rooms (Standard Rooms)
In rooms without ceiling-mounted equipment supported by Air-FRAME, the ceiling height is the line between where the aluminum lighting grid meets the lighting lens:
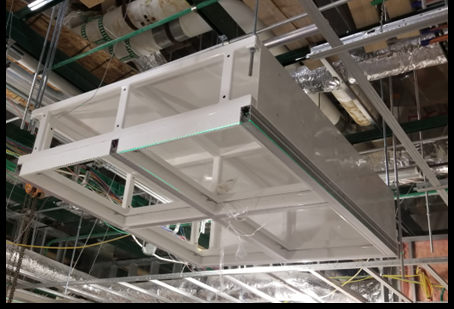
Figure 13: AirFRAME® module hanging with laser
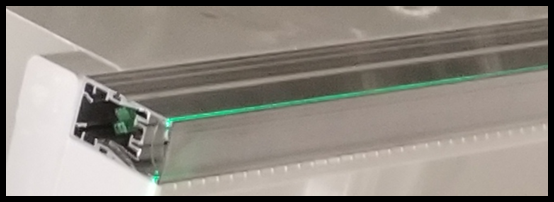
Figure 14: Close view of finished ceiling reference on AirFRAME® module
Hybrid Operating Rooms (Ceiling-Mounted Imaging Equipment Rooms)
In rooms
with ceiling-mounted equipment supported by AirFRAME, the elevation is tied to the position of the
Unistrut Embeds that support the ceiling mounted imaging equipment.
ALERT: Tolerance Is Critical
Imaging equipment manufacturers typically require precise distances from the top of the table floorplate to the bottom of the Unistrut embeds. If the AirFRAME is mounted too low, the Unistrut cannot be adjusted upwards more than 0.5mm (by removing pre-installed shim).
It is better to hang slightly high than too low.
Once the imaging equipment manufacturer's representative comes to verify Unistrut height, the hard-lid ceiling and flooring is typically installed so it can be VERY expensive to raise the whole AirFRAME system or grind the floor and re-install the table plate at that point.
AirFRAME Unistrut Embeds are adjustable in height for small adjustments. Systems ship with a 0.5mm shim pre-installed and extra 0.5 and 1mm shims are sent "loose" for field adjustments. Unistrut Embeds can be shimmed downwards by inserting shims but can only be adjusted upwards 0.5mm by removing a single shim. Therefore, it is better to err on hanging too high rather than too low.
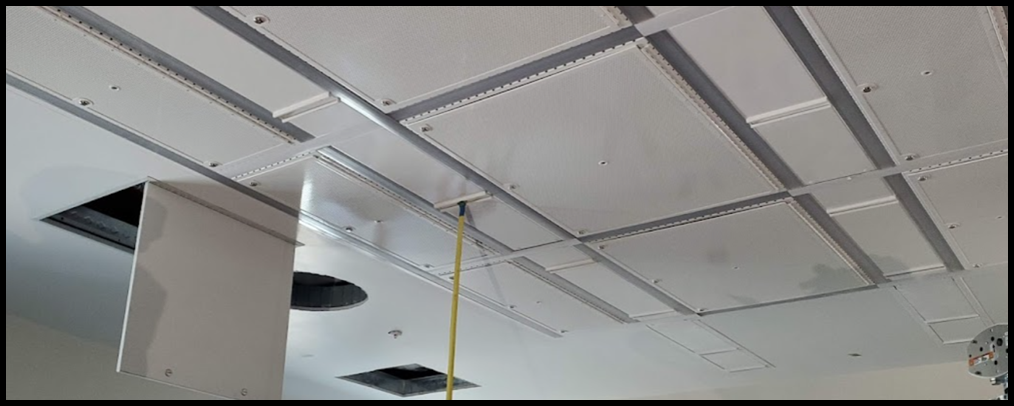
Figure 15: Measuring Unistrut height on AirFRAME®
Receiving, Inspection, and Storage
Most projects involve multiple ORs with multiple AirFRAME modules per room. Therefore, it is important to keep units wrapped until they are ready to be moved into the OR where they will be installed. The tag numbers on the wrapping provide the most expedient way to identify module groupings by OR, so it can be helpful to group modules by room before beginning to move or unwrap them.
Moving Modules
ALERT: Center of Gravity and Safe Handling:
When lifting and moving modules, ensure the module is centered and stable on forks before moving.
Move slowly and deliberately to prevent tipping or shifting.
Keep the area clear of personnel during lifting and movement to avoid injury in case of unexpected module shift.
Preparing Modules for Movement
- Place shipping pallet on flat, even surface
- Remove stabilizing lumber
- Unscrew and discard any blocking or bracing attached to the pallet
- Most screws use a #2 Philips bit (bit not provided)
- If a T20 Torx bit is required, SLD provides it. It is usually stapled to the Bill of Lading (BOL) paperwork or attached to the boat wrap on the module and labeled as such.
Figure 16: BOL containing T20 bit stapled to paperwork
- Cut the banding straps securing the modules
WARNING: Banding Release Hazard
When cutting banding, components can shift unexpectedly. Keep all personnel clear of the immediate area in case modules move.
- Using forklift or telehandler, lift one module at a time from the pallet and place it onto staging blocks or moving dollies.
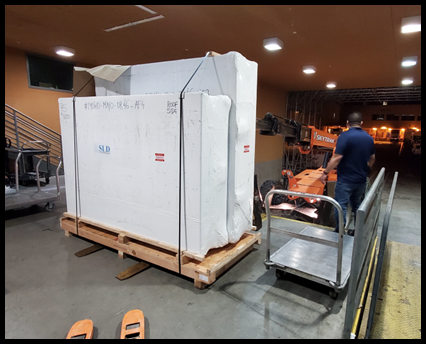
Figure 17: AirFRAME® module on telehandler in loading dock
INSTALLER TIP: Fork Protection
If boat wrap is removed or if placing modules directly onto forks, protect the metal surface with foam, carpet, sheeting or other material to minimize metal-on-metal contact that may scratch or damage the powder-coated finish.
Moving with Dollies
Once on moving dollies, modules may be wheeled to the work area. For heavier modules, use straps to secure the module to the dolly to prevent the unit from slipping during transport.
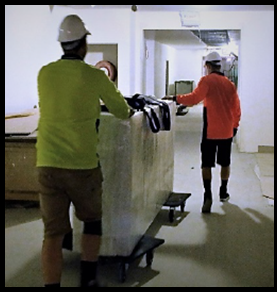
Figure 18: AirFRAME® module on moving dolly without straps
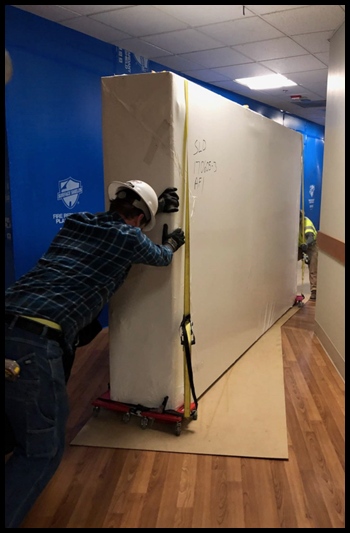
Figure 19: AirFRAME® module on moving dolly with straps
Alternatively, you can place the whole shipping pallet on dollies and move the whole pallet into the workspace if space allows.
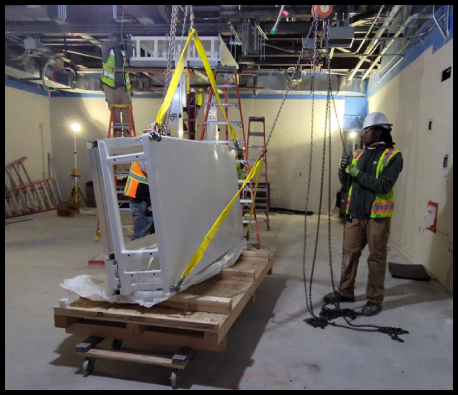
Figure 20: AirFRAME® module on shipping pallet in room
Unwrapping Modules
AirFRAME® modules are meticulously cleaned at the factory, packed with desiccant to prevent moisture intrusion, then double-wrapped in plastic, and sealed with boat wrap.
ALERT: Environmental Control During Unwrapping Required
DO NOT unwrap AirFRAME® modules in dirty, dusty or wet environments. Modules must be unwrapped only in a clean, dry area to prevent contamination or damage.
- Taking care not to scratch the powder-coated finish, use a utility knife (a hook-blade is ideal) or similar to cut the wrapping along the top and side edges of the module.
- Fold the wrapping down and away on both sides of the unit.
- Cut wrapping along the bottom edge to remove the excess wrapping.
- This will leave a small patch of wrapping that the module is sitting on. This can be removed once the module is lifted or tipped.
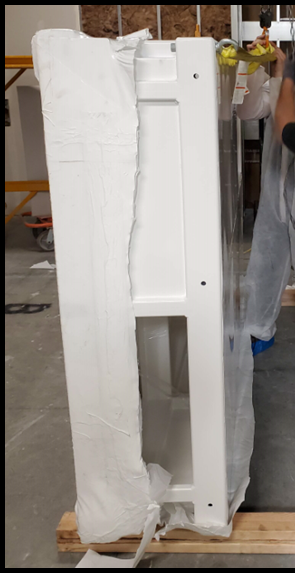
Figure 21: AirFRAME® module partially unwrapped
WARNING: Personal Injury and Equipment Damage Hazard
Use extreme caution when removing protective wrapping.
Improper handling can result in:
- Personal Injury (e.g., cuts from tools, slip/trip hazards caused by loose plastic)
- Damage to the powder-coated finish, which may compromise the integrity of the metal frame
Dispose of plastic wrapping and debris promptly and properly as you work. Do not allow packaging materials to accumulate in the work area.
Remember: AirFRAME® is medical-grade equipment. It must arrive clean, unmarred, and sterile-ready to ensure the safety of surgical patients below.
Hanging Modules
WARNING: Use Only Properly Rated Lifting Equipment
Before lifting, verify that all hoists, slings, rigging, and lifting devices are rated to support the full weight of the load.
Failure to confirm lifting capacity may result in serious injury, death, or significant property damage.
It is the responsibility of the installer to ensure compliance with all applicable OSHA and ANSI standards for safe lifting and rigging practices.
For verified module weights, reference the project submittal, contact your SLD Project Manager or email
support@sldus.com.
WARNING: Verify Suspension Hardware Load Ratings
Before installation, confirm that all suspension hardware, including rods, anchors, washers, and nuts, is rated to support the full weight of the AirFRAME® system with the required safety factor.
Failure to verify load ratings may result in structural failure, serious injury, or death.
Follow all applicable OSHA and ANSI standards for overhead lifting and support systems.
Protect Material Lift Forks
Unprotected material lift forks will damage the finish face of the AirFRAME module. To prevent scratches, gouges or other surface damage, cover the forks with foam, carpet, sheeting, or other protective material. Foam sheets shipped between AirFRAME modules can be reused for fork protection (see Figure 22). Additionally, inspect for bolts, nuts, flanges, lips, or other protrusions that may extend into the space of adjacent modules. These obstructions can cause scratching, denting, or alignment issues during installation. (Refer to Figure 23 for an example of potential interference and resulting damage).
Figure 22: Material lift with foam on forks
Figure 23: Material lift protrusion clash with resulting damage to adjacent module
INSTALLER TIP: Fork Protection
Use a full standard pallet on each material lift with SLD packing foam on top to provide a large, even surface for modules to sit on (See Figure 28).
Attach foam to a long 2x4 between forks and module (See Figure 33).
Positioning Chain Hoists
Before manipulating modules, install two chain hoists in the ceiling, spaced at or slightly wider than the width of the largest module. Position chain hoists off to the side of the room or otherwise outside the central work area to avoid obstructing the lift-in path. When possible, perform all module manipulation in a single location to minimize time spent relocating hoists.
Acceptable mounting methods for chain hoists include:
- Beam clamps attached to structural beam or steel
- Lifting straps securely wrapped around a structural beam or steel
- Eye bolts connected to a turnbuckle, which is then secured to a suspension rod
Figure 24: Chain hoist secured to beam with strap
Figure 25: Chain hoist secured to beam clamp
CAUTION: Unbalanced Load Risk When Using a Single Hoist
A single properly-rated chain hoist can be used. However, when using only one hoist, modules will be less balanced during rotation and may quickly drop or "fall" into the flat position. Use extreme caution to control movement and prevent injury or equipment damage.
Rotating Modules
AirFRAME® modules are shipped in a knife-edge orientation and must be rotated to a flat orientation before placement on a material lift.
SLD provides loose 5/8" eyebolts for most modules and/or manufactured lifting lugs for heavier modules.
Eyebolts are the most common solution; lifting lugs are supplied only when the module’s weight exceeds the safe working load of the eyebolts (rare).
Recommended Method
1. Install lifting points
Install eyebolts or lifting lugs into the suspension points on opposite corners of the module.
Figure 26: Lifting point locations on AirFRAME module
2. Attach lifting equipment
Connect a chain hoist to each eyebolt or lifting lug.
3. Rotate the module
Operate both chain hoists slowly, raising the lower end faster to bring the module into a flat position.
Assign one installer to guide and stabilize the module during rotation.
Figure 27: Rotating a module on chain hoists
4. Transfer to material lifts
Once the module is flat, position material lifts beneath it.
Raise the lifts until they take the full weight of the module from the chain hoists.
5. Remove chain hoists
Detach both hoists from the lifting points.
6. Position for installation
Move the module on the material lifts to the exact location beneath the installation point.
Figure 28: AirFRAME® module on material lifts
Alternate Methods
ALERT: Avoid Pressure on Module Edges
The following methods are less desirable because they place pressure on the lighting grid or air delivery frames.
This pressure can result in damage to these components.
Figure 29: Rotating module with single hoist onto material lifts
Figure 30: Rotating module with material lift hoist attachment
Figure 31: Rotating module using straps through vertical uprights in module
Figure 32: Rotating module down onto floor, then picking up to place on material lift
Lift Into Place
1. Raise the module
Using properly rated material lifts, raise the module evenly.
Continue lifting until the module is aligned with the suspension rods.
2. Prepare the suspension rods
Ensure a top nut is threaded onto each rod above the point where the top of the AirFRAME® will land.
Guide each suspension rod through a fender washer and into the suspension holes as the unit is raised.
INSTALLER TIP: A fender washer can be temporarily taped to the pre-installed top nut and lowered into position later to simplify alignment.
Figure 33: Module being installed
3. Secure the module
Once each rod is through its corresponding suspension hole:
- Install the SLD-supplied plate washer
- Add a fender washer
- Thread a nut to secure the AirFRAME to the rod
- Optional: Thread a second nut on to act as a jam nut
Figure 34: Proper hardware stack
Figure 35: Lower hardware with optional jam nut
4. Adjacent Modules
When hanging adjacent modules, take care not to pinch, cut, crush, or otherwise damage the module-to-module wiring.
Tuck the wiring into the lighting grid so it can be accessed and connected later.
See Module-to-Module Connections section for further details.
5. Final leveling
If possible, leave the top nuts slightly loose until the entire system is level.
Once leveling is complete, tighten all top nuts to lock the module in place.
ALERT: Suspension Hardware Requirements
Refer to the
project-specific Structural Calculations, interstitial framing design as well as the suspension point page of the ship loose drawings for the correct
suspension hardware type, size and installation method.
Using incorrect hardware may result in structural failure or non-compliance with engineering specification.
INSTALLER TIP: All-Thread Rod Preparation
Feeding suspension rods through the module's suspension holes is easier if each all-thread rod drop is cut to a slightly different length
This staggered length approach prevents the need to align and feen all rods simultaneously, reducing the risk of binding or misalignment during installation.
Figure 36: Staggered ATR cut lengths
IMPORTANT NOTICE: Linked Video Disclaimer
Linked videos are provided for reference only and are intended to supplement this installation manual.
They do not replace the written instructions, safety requirements, or project-specific documentation.
Always follow the procedures, specifications, and safety standards outlined in this manual and in the project’s approved documentation.
System Leveling, Finished Ceiling Height
Standard Rooms
1. Level the first module
Begin installation with one module.
Verify that it is level and aligned to the finished ceiling plane as defined in the project-specific drawings.
If the module is not level, adjust the lower suspension nuts of the module until level and at correct elevation on all sides.
2. Monitor dimensions during installation
Continuously check each installed module against the overall SLD dimensions to ensure compliance with project specifications.
3. Final securement
When the entire system is fully level and dimensionally correct with module-to-module bolts installed:
- Tighten all nuts securing modules in place to prevent movement. (See Module-to-Module Connections section for important considerations)
- Trim all-thread rod if required.
Module-to-Module Connections
Lighting System Connections
The AirFRAME® lighting system uses wiring quick-connects at module-to-module locations. Making these connections is the responsibility of the installing contractor.
IMPORTANT NOTICE: Avoid Wiring Damage During Installation
When hanging modules, take care not to pinch, cut, crush, or otherwise damage the wiring or connectors.
Damaged wiring can lead to system malfunctions.
Connection Methods
1. Connection While Hanging:
- With modules suspended from their all-thread rods before bolted together, separate them enough to access the wiring.
- Make the quick-connect wiring connections making sure the wires are seated into the connector securely and the connectors make a solid connection with each-other.
- Carefully allow the modules to move back into place, ensuring no wires or connectors are pinched between them.
Figure 37: Module-to-Module wiring between modules
2. Connection from Lens Access
- Remove the lighting lens by prying it down from the edges.
- Remove the plastic retaining clip by pressing up and inwards on the tab.
- Pull the lighting strut down to expose the connection point behind the lighting strut.
- Make the quick-connect wiring connection.
- Replace the components in reverse order.
Figure 38: Lighting assembly removal
Bolted Connections
SLD supplies all hardware required for module-to-module bolted connections. Standard connections typically use 1/2" hardware, but sizes may vary. Refer to the project-specific ship loose drawings for the exact hardware quantities and sizes for your project.
Each bolting location includes:
- 1 bolt
- 1 washer (placed on the bolt-head side)
- 1 locking flange nut
Bolt lengths are provided as follows:
- 5" long bolts - For connecting 2" thick internal tubes to 2" thick internal tubes
- 4" long bolts - For connecting 1" thick internal tubes to 2" thick internal tubes
INSTALLER TIP: Leave Hardware Loose for Alignment
When hanging modules, install the hardware but only thread the nut on a few turns onto the bolt. This will make it easier to align additional modules. Tighten all hardware only after all modules are installed and the system is fully level.
ALERT: Tightening Requirement - "Snug-tight"
All module-to-module bolts must be tightened to Snug-tight in accordance with RCSC 2020, Section 8.1 (or the most current revision).
Definition:
"Snug-tight is the condition that exists when all of the plies in a connection have been pulled into firm contact by the bolts in the joint and all of the bolts in the joint have been tightened sufficiently to prevent the removal of the nuts without the use of a wrench." -- RCSC 2020, Section 8.1
Failure to meet this requirement may result in joint loosening, structural instability, or equipment damage.
WARNING: Do Not Over-Tighten Bolts
Over-tightening beyond the Snug-tight condition can cause:
- Crushing of tube walls
- Distortion of the connection
- Damage to the powder-coated finish
- Premature failure of hardware
Tighten only to the Snug-tight requirement as defined by RCSC 2020, Section 8.1 (or most current revision).
Rivet Connections
If the AirFRAME® system has been designed with more than one air delivery module, frame rivets are required (#42BRAW).
At every location where two air delivery modules meet, the frame(s) on one side of the module-to-module spit must be riveted to the lighting grid on the opposite side.
Using a manual, pneumatic, or electric rivet gun:
- Rivet the frame(s) securely to the grid with the supplied frame rivets.
- Confirm that each rivet forms a solid connection.
- Ensure the frame remains flush against the grid after riveting.
Figure 39: Module-to-module rivets
ALERT: Riveting Step Cannot Be Skipped
Failure to complete this step will prevent HEPA filters from seating correctly, which can result in leakage around the filters.
This compromises system performance and sterile environment integrity.
Caulking Requirements
It is critical that the modules be installed tight against one another as noted in the Module-to-Module Connections section. The alignment is the responsibility of the installing contractor.
Surface Preparation:
- Maintain protocol-level cleanliness before applying caulk.
- Thoroughly clean all surfaces where caulk will be applied using IPA wipes.
- Follow proper PPE requirements as required.
Priming:
- Apply an approved primer — Dow Corning OS 1200 Primer — to all surfaces that will be caulked.
- Follow manufacturer instructions for required cure time before applying caulk.
Caulking Seams
- Use only SLD-supplied DOWSIL 732 Multi-Purpose White (300 mL) caulk.
- Apply a continuous bead along all internal seams.
- Tool the bead immediately after application using a gloved finger or smoothing tool, pressing the bead firmly into the seam to achieve a complete seal.
- The tube seams must be completely continuous — this seal is the final barrier to the sterile field.
Caulking Bolt Locations
- Caulk all bolt locations and structural plate washers, ensuring a full 360° seal.
- Caulk around all screw tips using SLD-supplied screw tip covers (See Module Penetration Protection section).
Curing
- Allow the caulk to cure for 24 hours.
- At 24 hours, the caulk should be cured to a depth of approximately 3mm.
Inspect all Caulking
- After curing, inspect all seams, penetrations, and hardware for any missed, broken, incomplete or thin caulk lines.
- Re-caulk any deficient areas using SLD-supplied caulk.
- Confirm all joints are sealed with a complete, unbroken bead.
Figure 40: Caulked module-to-module bolt
Figure 41: Caulked suspension bolt and washer
Module Penetration Protection
SLD Technology supplies screw tip covers (#3-142-100-TP) for any potential screw penetrations into the sides and top of AirFRAME® modules. These covers must be installed to protect the sterile air delivery path from contamination or leakage.
Installation of Screw Tip Covers
After installing any screws that penetrate the module walls within the air delivery area of the AirFRAME:
- Put a dab of caulk into the screw tip cover.
- Twist the cover securely onto the exposed screw tip.
- Ensure the cover fits tightly and completely seals the penetration.
Figure 42: Screw tip covers
Figure 43: Caulked screw tip cover
Important Note: Seal Unused Holes
Any unused pre-drilled holes that go through into the air path should be sealed (with a screw or cover)
Corner Cap / Split Cover Installation
Figure 44: Installed corner cap
NOTE: Parts Being Phased Out
Corner caps and split covers are being phased out but may still be included on some projects. Aways check the ship loose drawings for project-specific details.
ALERT: Sealing Required
Every corner cap and split cover must be sealed to prevent air leakage to or from the interstitial space.
Installation Procedure
1. Apply Caulk Seal
Apply a continuous bead of SLD-supplied caulk to the back side of the cap or cover
The bead must pass completely around the outside of the screw holes and finish where it started with no gaps in the seal
2. Position the Cap/Cover
Align the cap/cover with the AirFRAME® sidewall
Press the cap/cover into place, ensuring the caulk bead remains intact and unbroken.
3. Secure with Self-Tapping Screws
Using the provided self-tapping hex-head screws, fasten the cap/cover through the pre-punched screw holes.
4. Protect Exposed Screw Tips
On the inside of the AirFRAME®, cap all exposed screw tips (see Module Penetration Protection section for details).
5. Final Seal Inspection
Verify that the caulk seal between the cap/cover and the AirFRAME® sidewall is continuous
Fill any voids or gaps with caulk to ensure a fully sealed joint.
Final Cleaning
HVAC Blowdown
SLD Technology recommends performing a 24-48 hour “blowdown” of the HVAC system to be performed after "dirty" work in the room is complete and before final cleaning, Damper-Diffuser door installation or HEPA filter installation. This helps remove dust and construction debris from the ductwork and prevents contamination of the diffusers and filters.
If Damper-Diffuser doors have already been installed, open them and let them hang down while this blowdown is performed.
Cleaning
Vacuum and clean the grid, inside of the air delivery can, Damper-Diffuser doors, and screens of all foreign objects and debris.
Wipe down all inside surfaces (excluding lighting lens) with IPA wipes.
IMPORTANT NOTICE: Light Lens Cleaning
Clean light lens material only with 100% deionized water. Do not use alcohol, ammonia-based cleaners, or any other cleaning agents. These can cause immediate and irreparable damage to the lens material.
Damper-Diffuser (DD) Door Installation
Handling and Preparation
- Keep DD doors in their crate and protected until installation.
- DD doors are long-lead items and expensive to replace individually.
- Handle carefully to avoid bending or damage to the diffuser screen.
- Install using two people.
Installation Procedure
1. Locate Components
Find the DD rivets (#45BRAW) and the hinged DD door assembly.
2. Align Hinges
On the hinge for each DD door, locate the set of rivet holes.
Align these holes with the corresponding holes in the DD frame around the vent opening.
These holes are only located on one side, so the DD door can only be installed in the correct orientation.
3. Rivet Hinges in Place
Using a manual, pneumatic or electric rivet gun, secure the DD door hinge to the frame with the DD rivets.
Ensure each rivet makes a solid connection and that the hinge remains flush against the lower side of the frame.
Figure 45: DD door installation
4. Preload the DD Door
Fully open the DD door and let it hang downward.
Gently apply pressure to bend the diffuser screen backwards to create a slight arc in its frame. See Figure 46.
This step compensates for settling during shipment and prevents sagging.
⚠️ CAUTION: Do not apply excessive pressure—DD screens are easily damaged.
5. Close and Lock the DD Door
Close the DD door and engage all cam locks to secure it in place.
Verify that the diffuser screen sits flush against the frame.
6. Adjust if Necessary
If there is a noticeable gap, repeat steps 4 and 5 until a proper seal is achieved.
Figure 46: Damper-Diffuser door preloading
Installation Timelapse Videos
IMPORTANT NOTICE: Linked Video Disclaimer
Linked videos are provided for reference only and are intended to supplement this installation manual.
They do not replace the written instructions, safety requirements, or project-specific documentation.
Always follow the procedures, specifications, and safety standards outlined in this manual and in the project’s approved documentation.
Electrical Systems
HEPA Filters
WARNING: HEPA Filter Fragility and Handling
HEPA filters are fragile, sensitive to moisture/temperature, and require strict handling and storage protocols.
Improper handling or storage can cause filter damage, leading to loss of filtration integrity and failure to meet clinical air cleanliness requirements.
Always follow the filter manufacturer’s handling instructions for transportation, storage, and installation.
ALERT: Responsibility for Filter Care
SLD Technology is not responsible for any damage to HEPA filters caused by improper storage or handling after delivery.
Notify SLD Technology immediately and notate on BOL if shipment arrived damaged in any way by contacting SLD Support at:
support@sldus.comReceive and Inspect
- Prepare the site to accept and properly handle HEPA filters.
- Filters purchased through SLD are drop-shipped directly from the filter manufacturer; therefore, SLD cannot provide a 24-hour delivery notice.
- Inspect the skids and crates for any shipping damage. Notate on BOL and notify SLD immediately, support@sldus.com.
- Store filters indoors (under roof and enclosed) in a clean, dry, climate controlled space, and absolutely protected from moisture.
Room and Personnel Preparation
Before breaking the wrapping seal on HEPA filters:
- Ensure the operating room is clean and free from construction debris or airborne contaminants.
- All personnel must wear OR-appropriate PPE, including:
- Cleanroom coveralls, scrubs, or bunny suits
- Hair and beard covers
- Shoe covers
- Clean, powder-free gloves
- Avoid touching the filter media at all times.
Installation Procedure
1. Position for Access
- Install HEPA filters before installing the Damper-Diffuser (DD) doors, or:
- Open the DD cam locks.
- Lower both the diffuser and damper to hang down for access.
2. Follow Filter Manufacturer’s Instructions
- Handle filters only as directed by the filter manufacturer.
- Do not rack or twist the filter frame.
- Do not apply pressure, even light hand pressure, to the filter media.
- Two-person handling is recommended to reduce the risk of damage.
3. Prepare Filter Retention Tabs
- Rotate the filter retention tabs so that they clear of the diffuser knife edge.
4. Position and Seat the Filter
- Handling only by the aluminum frame, position the filter under the opening with the gel seal facing upwards.
- Lift the filter upwards into the opening, aligning the gel seal with the downward-facing knife edge.
- Push up on the filter frame only (never the media) to ensure a proper seal between the gel and the knife edge.
5. Secure the Filter
- Rotate the filter retention tabs perpendicular to the grid to support and hold the filter in place. See Figure 47.
- If a tab is difficult to rotate into position:
- Loosen the tab with a #2 Philips screwdriver
- Position the tab correctly
- Retighten the screw to secure the tab.
6. Removal
- Reverse the above steps to remove the filter.
Figure 47: Filter installation
Room Balancing
The AirFRAME® system should be balanced similar to a cleanroom rather than a traditional multi-diffuser operating room. Our Single Large Diffuser (SLD) array design functions more like cleanroom airflow system, and therefore requires specific balancing techniques.
Recommended Balancing Method:
- Use a Velgrid with 4 or 6" standoffs for velocity measurements.
- Flow hoods are not recommended as they can make room balancing more difficult.
- Take measurements at least 2" from the air pressure equalization ports on either side of the lighting channels.
- Calculate an average velocity across the full array to achieve proper balance.
- Target velocities are listed on the Submittal Drawings.
- For more information or technical guidance on room balancing, contact SLD Support at: support@sldus.com.
Damper Adjustment
All damper balancing components are downstream of the HEPA filter and can be adjusted without removing ceiling diffusers.
- Insert a hex key wrench though the center hole of the Damper-Diffuser screen and into the damper mechanism.
- Turn the hex key to adjust the guillotine slide plate to the desired position.
- Remove the hex key after adjustment.
Figure 48: Damper Adjustment
SLD Technology includes a limited standard warranty which is in effect for eighteen (18) months from date of shipment or twelve (12) months from date of installation, whichever occurs first. An extended 10-year warranty is also available. Reference the project-specific Submittal for full warranty terms and conditions. For more information, contact SLD Support at:
support@sldus.com.
Figure 49: Submit a ticket online
Copyright © 2025 SLD
Technology, Inc.
All rights reserved.
AirFRAME®, LEDiffuser®, uLED®, AirFRAME-LT® and associated marks are trademarks of SLD Technology, Inc.
Unauthorized reproduction, distribution, or use of this manual or any portion
thereof is strictly prohibited and may violate applicable laws.
SLD Technology reserves the
right to make changes to products, specifications, or this manual without
notice. The information herein is believed to be accurate at the time of
publication; however, SLD assumes no responsibility for errors, omissions, or the
consequences of use.